Introduction
Energy Harvesting (EH) is the process of extracting small amounts of energy from environmental sources to power a range of electronic devices. A typical application would be a sensor collecting environmental data and making it available wirelessly. For its potential of delivering energy autonomy, Energy Harvesting is seen as an enabling technology for the Internet of Things (IoT).Initially seen as a fit-and-forget solution for monitoring processes, structures and the environment, Energy Harvesting is set to enter the consumer market due to the ubiquitous presence of wearable devices, designed to monitor physical workouts and health parameters and even sleep. A truly friendly 24/7 monitoring device must be self powered. Human motion is typically rather slow in comparison to the speeds required by electromagnetic generators (dynamo-like) or the capabilities of piezoelectric transducers. This suggests the need for …
Frequency up-conversion by plucking
The idea of frequency-up-conversion has now become mainstream in Energy Harvesting research and is typically implemented via impact (Umeda et al. 1996) or plucking (Kulah & Najafi 2004; Rastegar et al. 2006). In plucking excitation, the piezoelectric devices are ‘slowly’ deformed and then released; the principle is equivalent to the plucking of chords in a guitar (or a violin when the pizzicato technique is used). From the physical point of view, impact excitation involves the transfer of momentum; the principle is similar to hammers striking the wires in a piano. In Energy Harvesting practice, the two methods can sometimes overlap and a given excitation process can present characteristics of both in different degrees.
As seen in the figure, the plectrum plucks the bimorph, which means it gives it elastic energy by deforming it. Once released, the bimorph vibrates at resonance and converts this mechanical energy into electrical energy via the direct piezoelectric effect.
Both impact and plucking excitation, when applied to piezoelectric devices via mechanical contact, could potentially lead to damage since piezoelectric ceramics are brittle. This is one reason why contactless interaction between magnets has been investigated, although it would not be very difficult to protect the piezoceramics. More importantly, the Pizzicato² went magnetic to improve the quality of the release stage, which was observed to cause a major loss in efficiency (Pozzi et al., 2012).
The first version of the Pizzicato² energy harvester was designed for contact plucking via either kapton or steel plectra and it generated a maximum of about 5 mJ per running step (Pozzi et al. 2015).
Contactless plucking in Energy Harvesting
Having decided to go contactless via magnetic plucking, the next questions are: what magnets? what arrangement? at what distance?
The figure below represents the proposed geometry and the 3D mesh used in the Finite Element Model to predict the force experienced by the bimorph. The two blocks in the foreground are the magnets, the rest of the structure is made of soft iron.
FE results show that this arrangement is excellent and promises to get the most out of the bimorphs. So, the next step was to modify the Pizzicato² to take on this arrangement.
Pizzicato² contactless
The outer ring was CNC-milled out of soft iron. The 3×3×3 mm³ neodymium magnets were fixed to the end of the bimorphs with superglue (a tricky process requiring sub-millimeter accuracy).
The photo shows the Pizzicato² magnetic ready to be tested. It is mounted on an intelligent servomotor controlled to move in a way that replicates the motion of the knee during walking or running, viz. gait simulation.
The improvement in the energy generation was astounding! The table below reproduces some experimental data. Notice that the energy is from one single bimorph and the values are comparable with the energy from the original full Pizzicato² with steel plectra!
An interesting finding is that the energy harvested in one full revolution decreases if the speed is above 2-3 s/rev; this is in contrast with what was found with contact plucking, where, presumably, the release became sharper at higher speeds.
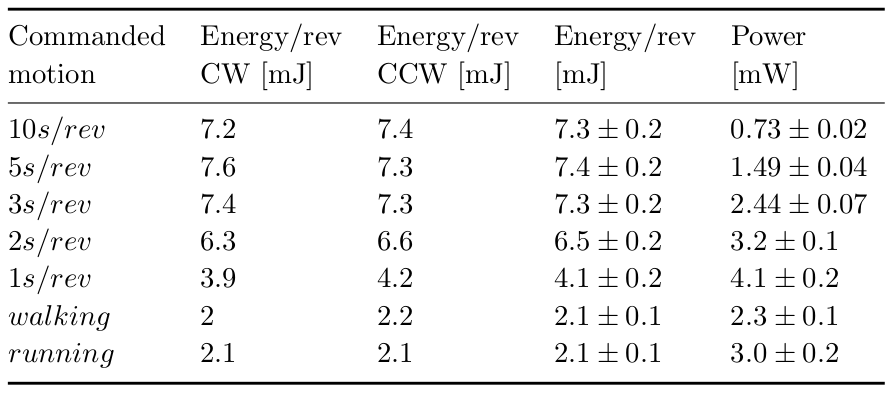
Energy and power produced by one bimorph in one revolution at a selection of speeds or in one step at the specified gait.
The striking difference between contact plucking and magnetic contactless plucking is made clear by the following table.
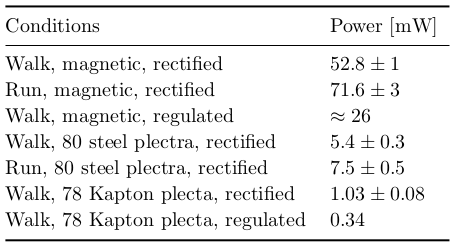
Summary of performance of the Pizzicato² knee-joint harvester. Data with mechanical plucking (Kapton and steel plectra) are taken from (Pozzi et al., 2015)
The “Walk, magnetic, regulated” power of 26 mW means that the Pizzicato² magnetic was able to produce a continuous current of almost 8 mA at a regulated 3.3 V, as would be required by many modern microcontrollers (which usually get it from a normal battery).
Conclusions
Piezoelectric energy harvesting is often taunted with being able to produce only tiny amount of electrical power. The Pizzicato², once it went contactless, reached the record output of almost 72 mW rectified power during running.
Contributors and external financial support
Dr. H.J.A. Almond (photochemical machining of steel plectra)
Dr. G.J.T. Leighton (passivation of the steel plectra)
B. Abraham (plotter cutting of the kapton plectra)
CranfieldNano (purchase of piezoelectric bimorphs, manufacture of PCBs and hub)
References
Kulah, H. & Najafi, K., 2004. An electromagnetic micro power generator for low-frequency environmental vibrations. In Micro Electro Mechanical Systems, 2004. 17th IEEE International Conference on. (MEMS), pp. 237– 240.
Umeda, M., Nakamura, K. & Ueha, S., 1996. Analysis of the Transformation of Mechanical Impact Energy to Electric Energy Using Piezoelectric Vibrator. Japanese Journal of Applied Physics, 35(Part 1, No. 5B), pp.3267–3273.
Pozzi, M. & Zhu, M., 2012. Characterization of a rotary piezoelectric energy harvester based on plucking excitation for knee-joint wearable applications. Smart Materials and Structures, 21(5), p.055004
Pozzi, M. et al., 2015. Low-profile and wearable energy harvester based on plucked piezoelectric cantilevers. In Proc. SPIE Smart Sensors, Actuators, and MEMS VII; and Cyber Physical Systems. Barcelona (Spain), pp. 951706–951706–9.
Rastegar, J., Pereira, C. & Nguyen, H.-L., 2006. Piezoelectric-based power sources for harvesting energy from platforms with low-frequency vibration. In E. V. White, ed. Smart Structures and Materials 2006: Industrial and Commercial Applications of Smart Structures Technologies. San Diego, CA, USA: SPIE, pp. 617101–7.
Awesome! Its in fact amazing information, I have got much clear idea regarding EH from this page!
Hello. impressive job. I did not anticipate this.
With thanks! Valuable information!
I have been checking out many of your stories and i can state pretty awesome.
I like the helpful info you provide in your articles. I will bookmark your weblog and check again here regularly.
I got what you mean,saved to fav, very decent site.
I’m quite certain I’ve learned lots of new stuff.